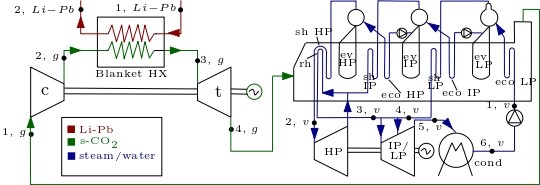
An optimized power conversion system for a stellarator-based nuclear…
A new scientific paper is published by the UNITUS Nuclear Fusion Research team, concerning the optimization of the power conversion system for a stellarator-based nuclear fusion power plant [1].
Unlike all other fusion devices, which are pulsed, the stellarator is inherently steady-state. Thus, it requires a different downstream power conversion system compared to tokamaks. Notably, the authors conceive and optimize such a system for a stellarator power plant, equipped with plasma-facing liquid metal walls in high temperature range (700-900°C). This allows to reach a high power conversion efficiency, due to possible coupling with a CO2 Brayton-Rankine Combined Cycle [2]. Notably, the use of supercritical CO2 for the topping cycle is recommended for high efficiency and low system volume. Following the experience of large scale CC plants, the bottoming cycle is a three pressure superheated steam cycle, with optional re-heating. The system is described through a custom lumped parameter model implemented within MATLAB/Simscape® physical modelling environment. Such a model is preparatory for the optimization via genetic algorithm of the relevant system parameters: the compression ratio of the Brayton cycle and the high, intermediate, and low pressures of the steam turbines.
The efficiency of the power conversion system results 51% and net electrical efficiency of the complete plant (including electrical consumption of reactor auxiliary systems) is 34%. Such figures are remarkably higher compared to the state-of-the-art designs in the field of thermo-nuclear fusion plants, considering that the most optimistic and recent estimate foresee a heat-to-power conversion efficiency of about 34% for tokamak-like reactors. Once the model is validated thanks to the comparison with the results available in the literature for similar systems [2-3], the engineering feasibility, despite the critical components not being market-ready, is discussed. Indeed, the preliminary design of the large-scale supercritical CO2 Gas Turbine and of the compact heat exchanger for the Brayton cycle is successfully carried out.
[1] F. R. Famà et al., “An optimized power conversion system for a stellarator-based nuclear fusion power plant”, Energy Conversion and Management, 276, 116572, 2023.
[2] S. Segantin et al., “Exploration of power conversion thermodynamic cycles for arc fusion reactor”, Fusion Engineering and Design, 155, 111645, 2020.
[3] B. Zohuri et al., “Advanced nuclear open air-Brayton cycles for highly efficient power conversion”, Nuclear Technology, 192, 1, 48–60, 2015.
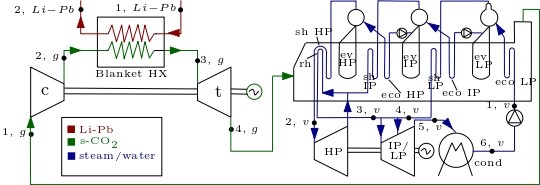