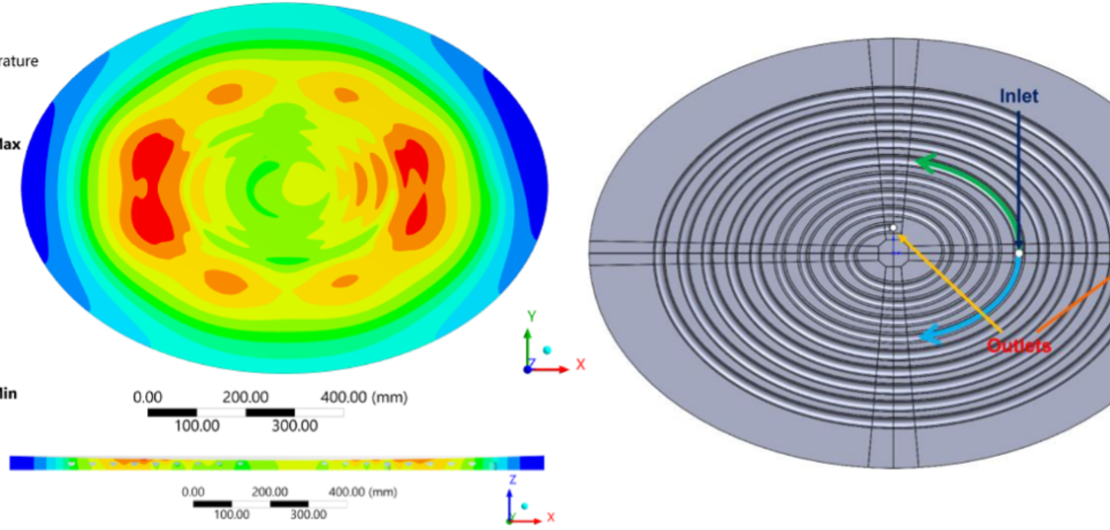
PRELIMINARY THERMAL AND STRUCTURAL ANALYSES ON THE PARABOLIC MIRROR…
A new scientific paper [1] has been published by the UNITUS Nuclear Fusion Research team, concerning the Italian facility “Divertor Tokamak Test” (DTT) [2]. The paper presents a preliminary study about the Parabolic Mirror of the multi-beam transmission line. The design of the mirror has a primary objective: to minimize the temperatures of the mirror and, consequently, the deformation caused by thermal expansion. This is aimed at reducing the impact on the losses in beam transmission efficiency. Various design options, such as materials, body thickness, and cooling solutions, including the shape of cooling channels and water flow, are explored, and discussed.
The mirror is focusing with a parabolic superior surface and has an elliptical shape. The first part of the work is about the realization of the standard CAD model, considering its main characteristics. This kind of structure is subject to the thermal load coming from the absorbed fraction of the microwave beams power, transmitted by eight beams, reflecting on its surface, simultaneously.
Different mirror models are compared. The first option considers an aluminium mirror. The second option is a Stainless-Steel (SS) mirror coupled with a copper layer. Both configurations foresee a simple cooling channel, with elliptical shape and only one turn. Two advanced options include improving the cooling channel, by introducing a cooling channel with a double spiral path, which increases the heat exchange area and allows for better temperature uniformity. An application is on a SS mirror coupled with a copper layer, whilst the second on a pure-copper mirror.
To compare the models evaluating the best performance, thermal and structural analyses have been carried out with ANSYS software and its embedded tool to simulate in a simplified way the water in the cooling channel.
The first results concern the trends of the time evolution of the maximum temperature. They are pairwise similar in two aspects: the reached peak and the cooling rate. The first two configurations with elliptical channel lead to higher peaks and slower cooling, while the spiral channel (third and fourth configurations) to lower peaks and faster cooling. In particular, the design with spiral channel and pure copper has a peak temperature of 55 °C, reduced by ~ 52 %, compared to the first configuration. This decrement of the temperature is good for the structural results. Indeed, from a structural point of view, the comparison of the Z deformation of all the configurations shows that the design in SS-Cu with elliptical channel is the worst solution and the design in pure Cu with spiral channel, has the best structural performance. The main reason is the high thermal conductivity of the copper and the wider heat exchange area possible with the spiral path. The maximum total deformation of this configuration is 0.140 mm, 83% lower than the first configuration (aluminium, with elliptical channel).
Having found the best solution among those proposed, an optimization was done in terms of thicknesses and hydraulic parameters.
The final configuration is a copper mirror with a bulk dug by a double spiral cooling channel, with the addition of a cover layer. The minimum total thickness of the mirror is 2 cm, including 4 mm (minimum thickness) of the cover layer. With an inlet water temperature of 30 °C and a mass flow rate of ~ 10 l/min for both spirals, the maximum temperature on the mirror is ~55 ◦C, recorded at the end time of the pulse of the beams. At the same time, the maximum total deformation is 0.140 mm. Although the highest temperatures occur at the end, the most critical moment in terms of deformation occurs approximately 34 seconds after the pulse begins, when the maximum total deformation reaches a value of 0.177 mm. The deformed geometry resulting from critical instants will be examined to analyse its impact on the propagation of beams.
References
[1] Salvitti, Alessandra, et al. “Preliminary thermal and structural analyses on the parabolic mirror of the Multi-Beam Transmission Line of the DTT ECH system.” Fusion Engineering and Design 200 (2024): 114106.
[2] R. Martone, et al., DTT Divertor Tokamak Test facility Interim Design Report, ENEA (2019).
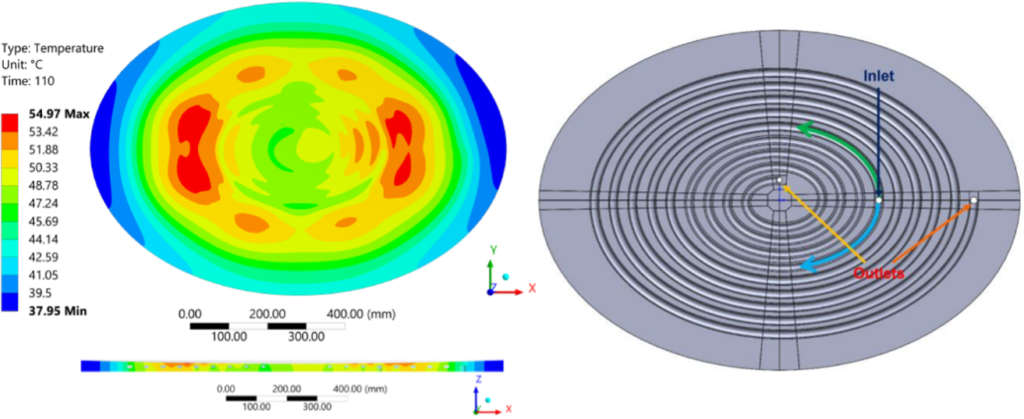