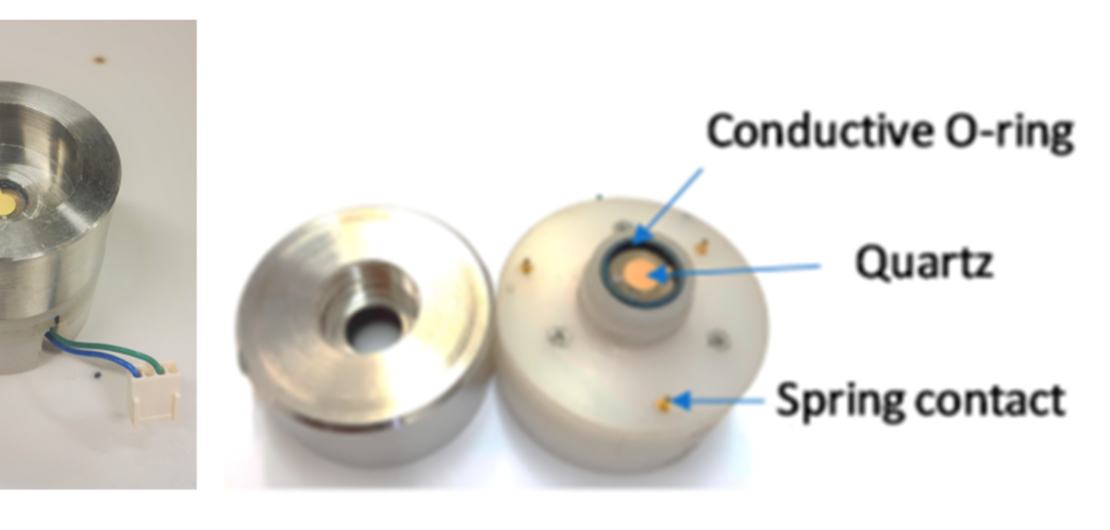
An Adaptive Measurement System for the Simultaneous Evaluation of…
In-liquid measurements with quartz-based sensors are used in many different application fields, among which are chemical sensing, biosensing and viscosity measurements [1,2,3,4].
Sensing systems based on quartzes exploit their electromechanical resonant behavior: their piezoelectric properties provide a transduction of mechanical quantities into electrical quantities, whereas the pure elastic behavior of the quartz, which is an almost ideal resonator, is extremely sensitive to the changes of mechanical properties (mass, stiffness and damping). These particular properties have been exploited to obtain many different sensors: the most traditional ones are Quartz Crystal Microbalances (QCM), operating as mass sensors with resolutions down to a few nanograms [5,6,7,8], although, if used in liquid environments, it is possible to employ resonant measurement systems to characterize liquid viscosity and density. In this contest, the use of resonant structures is widely diffused and spread in different applications. Just to mention a couple, García-Arribas et al. developed a magnetoelastic sensor to sensitively measure the viscosity of fluids, aimed at developing an online and real-time monitoring of the lubricant oil degradation in machinery [9], and Zang et al. used a self-oscillating tuning fork device to perform fast measurements of viscosity and density, with the aim of characterizing different phases of liquids in a multiphase flow [10]. Moreover, in several applications, the research interest is focused on the realization of distributed sensor networks using sensor fusion techniques [11,12,13].
The basic structure of a quartz-based chemical or biosensor is the QCM, which is usually an AT-cut quartz disk operating in the MHz range provided by two electrodes on the two opposite surfaces. When the quartz vibrates in air, it is possible to assume no damping, and the modal frequencies of the device are set by the disk thickness [14]. In particular, it can be written [15]: 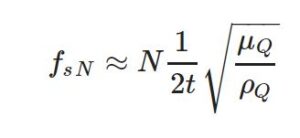
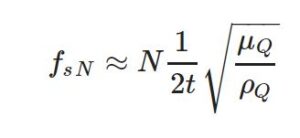
where fsN represents the N-th modal frequency, N∈ℵ and N odd and t is the thickness of the quartz, whereas ρQ and μQ are the quartz density and shear modulus.
A mass sensor is obtained by functionalizing one of the quartz surfaces with a material providing the selective adsorption of a target species. If, due to functionalization and to adsorption, a small additional mass (Δm) is deposited on one of the quartz surfaces, by assuming that the mechanical properties of the added layer are the same as those of the quartz, then the effect changes the resonator thickness and, accordingly, shifts the modal frequencies of a quantity (ΔfsN) related to the added mass: 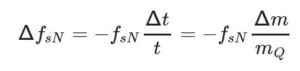
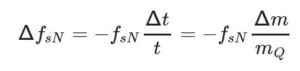
where mQ is the quartz mass, and the linear relation stems from the assumption of small thickness variations. Notice that Equation (2), written in a different form, is also known as the Sauerbrey equation [16].
By means of the piezoelectric effect, the mechanical vibrations are converted into an electrical charge or voltage signal. Therefore, a QCM is, in principle, a linear mass sensor providing the frequency as an output quantity. A typical 10-MHz AT-cut QCM provides, theoretically, a response of Δfs1(Hz)=−0.8 Δm (ng) [17].
A complete sensing system can be obtained by inserting the quartz into an electronic circuit providing the frequency metering [1].
Indeed, the measurement problem is far more complex [1,18]. First of all, the electromechanical vibrations can shift frequency not only due to the added mass (desired effect) but, also, due to the unwanted mechanical damping caused by the added layer, which has usually different and worse mechanical properties with respect to the quartz, especially in biosensors, where it consists of a lossy viscoelastic functionalization film and of the adsorbed target species (biological targets). Moreover, and more importantly, differently from AT-cut quartz oscillating in the air, where the surrounding medium can be well-described as an ideal fluid, and the standing elastic wave causing the vibration is confined in the solid disk, for in-liquid sensors, the surrounding medium is better described by a Newtonian fluid. In this case, part of the shear vibration can be transferred to the liquid and part of the elastic energy dissipated. The interaction with the fluid is, in this case, a non-negligible mechanical load (with both dissipative and conservative characteristics) that causes very large frequency shifts (up to hundreds of ppms). Due to this fact, some sensing systems exploit the dependency of the modal frequency of the quartz on the characteristics of the surrounding fluid to obtain viscosity measurements [14,19,20].
As a consequence, QCM-based measurement systems operating in liquid often couple the modal frequency shift assessment with the evaluation of the viscoelastic characteristics of the added layer through the monitoring of other dynamic parameters, such as the dissipation coefficient δ or, equivalently, the Q-factor [21,22]. This could unravel the inertial and dissipative behaviour of the ad-layer and enable distinguishing between the added mass and the surrounding liquid effects.
To continue with the issues related to the QCM-based measurements, it must be underlined that the way in which the vibrations are generated and measured can influence their frequency, which can be different from the searched modal frequency: for instance, the front-end circuit loads and influences the electromechanical resonance [1].
In a typical QCM system, the quartz is embedded in the feedback network of an oscillator circuit, and its output frequency is measured by, e.g., a digital frequency meter. QCM systems with dissipation monitoring (D-QCM) also provide a measurement of the dissipation factor δ (equivalent to the Q-factor) by inducing transients, e.g., disconnecting the feedback loop [23] and evaluating the transient decay duration. This allows for assessing the damping coefficient of the resonant electromechanical system.
In this paper, the problems related to measurements based on QCM in in-liquid applications are summarized, and a novel system based on a Meacham oscillator embedding an amplifier with adjustable gain is proposed. An automatic strategy is described that allows for gain tuning and maintaining the oscillator frequency close to the modal resonance of the quartz. From the adjusted gain value, an estimation of the series electromechanical resistance can be obtained, providing also the monitoring of the dissipative behavior of the electromechanical system through a robust estimation technique.
This paper is organized as follows: in Section 2, the operation of quartzes in liquid is presented, and the main measurement problems are discussed. In Section 3, the proposed oscillator topology, the series resistance estimation technique and the gain adjustment strategy are described. In Section 4, a prototype system, used to verify the proposed solution, is described, whereas Section 5 shows and discusses the experimental results. The conclusions are drawn in Section 6.
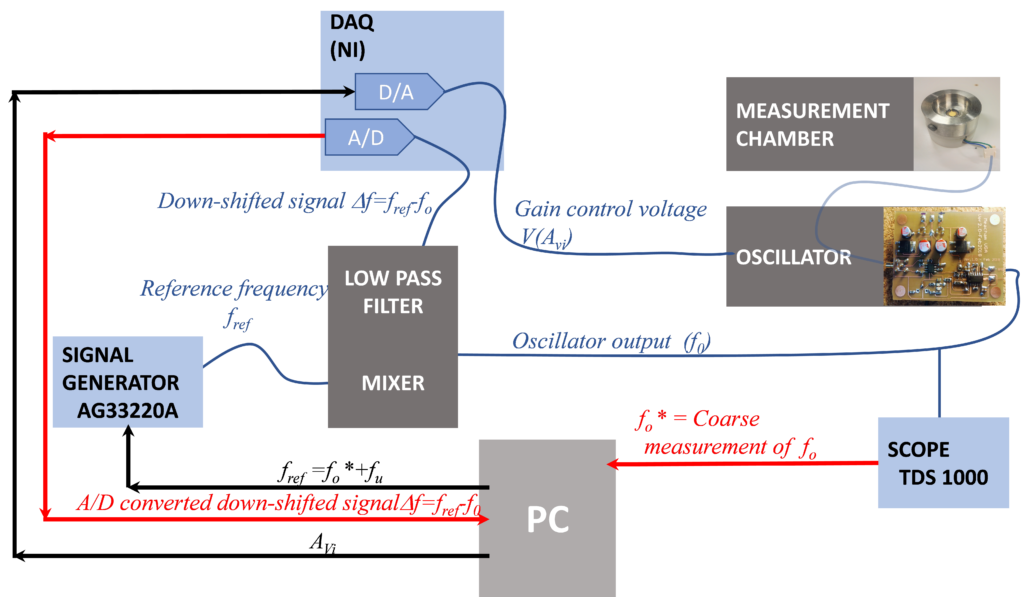