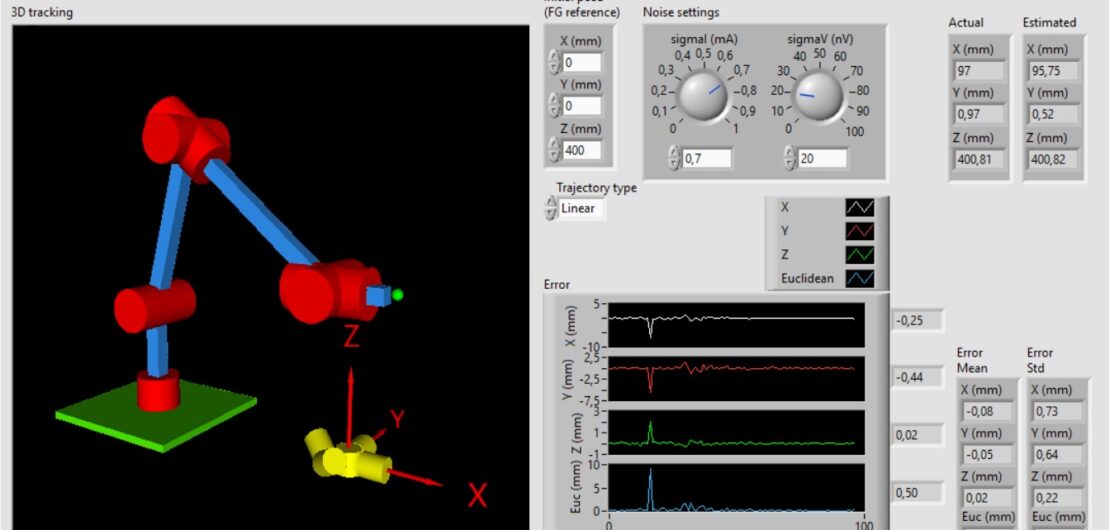
A virtual platform for real-time performance analysis of EM…
Background: Electromagnetic Tracking Systems (EMTSs) are widely used in surgical navigation, allowing to improve the outcome of diagnosis and surgical interventions, by providing the surgeon with intraoperative real-time position of surgical instruments during medical procedures. In particular, a very small magnetic sensor, which measures the magnetic field produced by a known field generator (FG), is inserted into the surgical instrument (e.g., a flexible instrument such as an endoscope or a needle), and the position of the sensor is estimated by means of a suitable algorithm.
Objectives: The main limitation of EM technology is the short tracking distance, which is generally no longer than 0.5 m from the FG in current commercial systems, due to the reduced amplitude of the magnetic field with distance, and the high sensitivity to EM interferences and magnetic field distortions, thus limiting tracking accuracy far from the FG. Many aspects affect system performance, and engineers and manufacturers should consider all of them, since also a small accuracy or distance increase is a valuable achievement in this field.
Methods: In this research, we propose a virtual platform for assessing the performance of EMTSs for surgical navigation, showing in real time how the various sources of error affect the accuracy of tracking distance estimation. The virtual platform is designed to be used in combination with a robot to move the sensor and provide accurate position references. The platform is composed of six main sections, and its functioning is illustrated in Fig. 1. The model of the EMTS if defined in an external file and imported into the platform, and the user defines the trajectory for sensor movement. Two different modalities can be performed: i) in the experimental mode, the platform connects to the DAQ device and the induced signal in the magnetic sensor is acquired as it is moved by the robot along the defined trajectory, ii) in the simulation mode, the signal of the magnetic sensor is simulated by employing a model of the magnetic field; in both cases, noise can be added to the signal. Finally, the position of the sensor is estimated by means of a suitable reconstruction algorithm, providing real-time 3D representation and error statistics.
Results: Simulations and experimental tests are performed to validate the proposed virtual platform in practical cases, showing its usefulness in assisting engineers during EMTS design and characterization, and by employing it to assess the performance of a real EMTS prototype (shown in Fig. 2), obtaining a mean Euclidean position error of about 2 mm at a distance of 600 mm from the FG, which is comparable with the ones obtained by simulations and suitable for many surgical procedures.
Conclusions: The platform provides a useful real-time tool to analyse EMTS components and field generator configurations, for a deeper understanding of EMTS technology, thus supporting engineers during system design and characterization.
References:[1] Ragolia, M. A., Attivissimo, F., Di Nisio, A., Lanzolla, A. M. L., & Scarpetta, M. (2021). “A virtual platform for real-time performance analysis of electromagnetic tracking systems for surgical navigation”. Acta IMEKO, 10(4), 103-110. doi:10.21014/acta_imeko.v10i4.1191.
[2] M. A. Ragolia, F. Attivissimo, A. Di Nisio, A. Maria Lucia Lanzolla and M. Scarpetta, “Reducing effect of magnetic field noise on sensor position estimation in surgical EM tracking,” 2021 IEEE International Symposium on Medical Measurements and Applications (MeMeA), Neuchâtel, Switzerland, 2021, pp. 1-6, doi: 10.1109/MeMeA52024.2021.9478723.[3] M. A. Ragolia et al., “EM tracking system for surgical navigation”, research project; https://www.researchgate.net/project/EM-tracking-system-for-surgical-navigation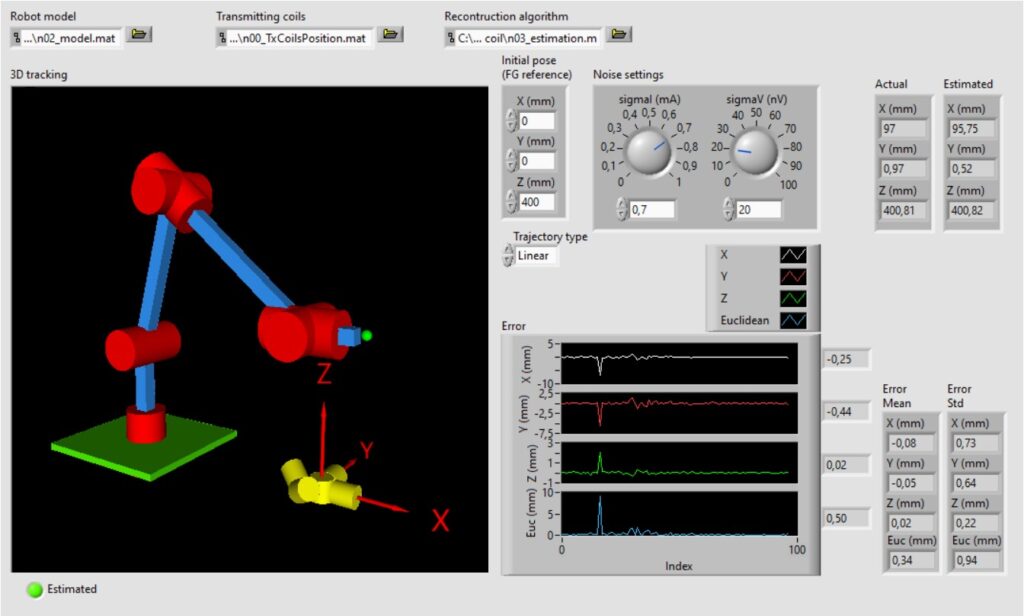
Virtual platform developed in LabVIEW, during the execution of a simulation. On the left: the model of the MELFA robot is shown during the movement; the green point is the position estimate provided by the algorithm, and FG reference system is shown in red. On the top: the noise settings section and the trajectory definition are shown. At the bottom: real-time statistics of position error are provided.
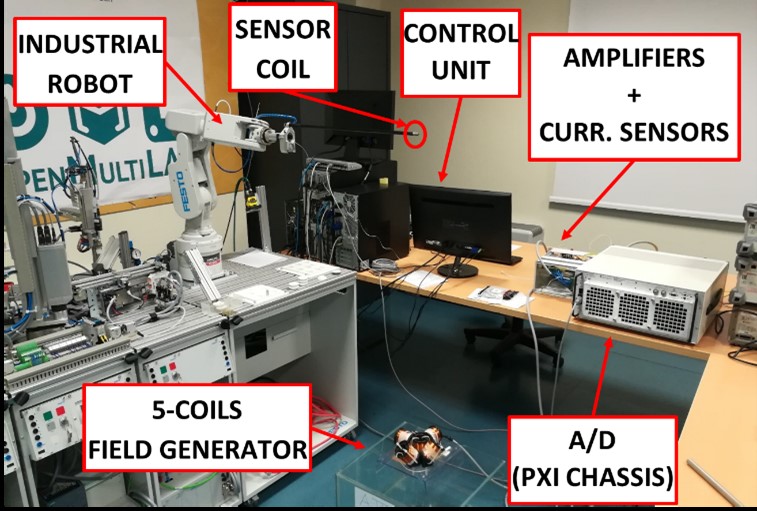
Experimental setup for system characterization. The developed prototype is composed of three main components: a Field Generator (FG), a Magnetic Sensor (MS) and a Control Unit (CU). The FG is composed of five transmitting coils, whose arrangement minimizes mutual inductances. Each coil is powered with a sinusoidal current at different frequencies (approximately from 1 to 5 kHz), thus generating an AC magnetic field. The whole magnetic flux generates an induced voltage on the MS, which is acquired, digitalized, and filtered by means of five band-pass filters thus obtaining five RMS voltage components, related to the different excitation frequencies. These components are used to estimate sensor position by means of a suitable reconstruction algorithm. The control software is developed in LabVIEW®, and the sensor is moved by means of an industrial robot (by Mitsubishi), which provides accurate position reference.